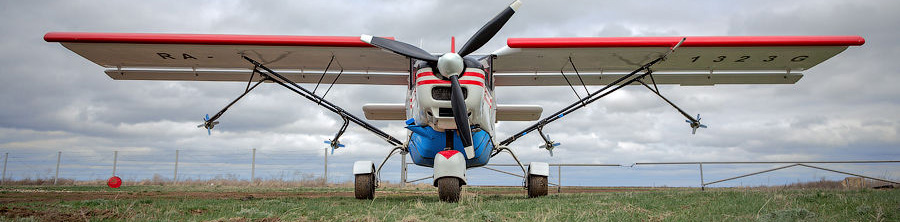
In 2015, the Novator airline entered the market with several developments for the most successful, in our opinion, for chemistry today, the SP-30 aircraft from the Spektr-Aero design bureau in Taganrog. These are a modification of the chemical equipment VDD-1-2000 SP, Cloud-N, a hydraulic front strut and windshield, equipment for aeroseeding. Everything in order. The chemical equipment has the same spray characteristics as the initial modification, but a serious revision of its weight, aerodynamic and layout properties has been made. The equipment is the same lightweight, maintainable and very durable tank with a capacity of 150 liters and a weight of 10 kg. But now not only the pump assembly is located on the tank, but also a system of shut-off valves (valves). The four VRZ nozzles remained the same disk, but due to a serious redesign of the structure, they became lighter and smaller, due to the reduction of the blades, which in turn reduces the drag. The equipment includes 2 sets of blades for a smaller and larger drop. VRZh is now not mounted on rods with struts, but occupy the same places with the help of more compact, easily removable brackets, installed on the wing struts without additional struts. The flow rate is controlled using the metering flow meter already presented on this forum. The equipment has been tested on all types of work for which it was intended (the introduction of herbicides, humates, poisons, desiccants, fungicides, bacteria) and showed itself from the best side. Due to the change in the design of the shut-off valves, the cut-off became faster and clearer and leaks are completely excluded. At the same time, the maximum speed of the aircraft with fully equipped equipment increased by 20 km / h compared to the previous modification. The equipment also includes a ground refueling complex with a motor-pump, designed to refuel an aircraft tank in a time of 1.5 to 3 minutes. The change in the layout scheme led to the fact that the removal of the equipment takes a very short time and consists of: undocking the clamps of the electrical equipment, removing the tank with attachments and 4 brackets from the STL, and the aircraft is completely free of attachments.
* this page has been translated automatically
Spraying Equipment for Ultralight Aircrafts
No wonder that in aerial spraying a lot depends on the equipment. Novator Company manufactures and sells aerial spraying equipment for ultra-low-volume spraying to mount on SP-30 aircrafts (manufactured by Spektr-Aero engineering center, Taganrog, Russia), CH-701 and other similar ultralight aircrafts.
The spraying equipment comprises:
- a chemical tank with a pump assembly
- booms with rotary disk atomizers (RDA)
- spraying system control units mounted in the cockpit (a handle on the control column with a button to open or close the spraying valves; a handle to control the mixing valve; a flow rate display)
- a land-based filling unit
The prototype of this system VDD-1-2000 (ВДД-1-2000) was developed by a team of authors (A. P. Kabakov, V. V. Lygin, M. G. Nikitin) in 2002 and was employed for aerial spraying first on hang-gliders and later on CH-701 and SP-30 aircrafts.
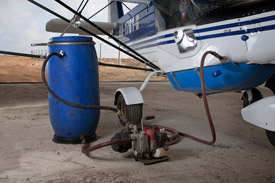
The system has been upgraded a few times since then, and its improved versions were certified three times by the civil aviation authority. The assessment and certification was conducted by PANH Research Institute experts (Krasnodar, Russia), who recognized that the system presented the best characteristics (spraying nozzles; mesh screen atomizers) for light and ultralight aircrafts in comparison with existing analogues.
The size of droplets dispersed by the rotary disk atomizers (RDA) is uniform and consistent (the maximum deviation from the specified size is 10%), which ensures equal speed of falling droplets and prevents quick evaporation of fine mist. Together with proper setting of the atomizers against the fuselage and wing, one will get the necessary density of coverage (15 droplets per square centimeter – uniform across the swath width) in any acceptable weather conditions.
The latest improvements to the RDA have increased the durability of the bearings (30-35 thousand hectares before replacement) and have ensured application of humates without frequent disassembling and cleaning the RDA (it is enough to flush water through the system after a working shift).

Upstream each RDA there is a shutoff ball valve and a flow control valve. The shutoff valves are activated through a single drive gear mounted under the fuselage and operated via control cables inside wing-shaped booms.
The chemical tank is mounted under the fuselage too. The tank is made of polypropylene, the chemical resistance of which is very high (significantly higher than that of aluminum or fiberglass). This material is not affected even by Chinese chemical agents, which, if applied at increased concentration, dissolve fiberglass hoppers after one working shift.
At the same time the tank with a capacity of 150 liters has a considerably lighter weight than its fiberglass and aluminum equivalents. Besides, it has a streamline shape, which in combination with wing-shaped booms significantly reduces the aerodynamic resistance of the agricultural version of an aircraft. Consequently, spraying can be conducted at lower RPM, which saves fuel and extends engine life.
The internal configuration of the tank prevents spraying fluid from leaking through the intake duct at any pitching moment, thus excluding any delays when the aircraft approaches a new spraying pass.
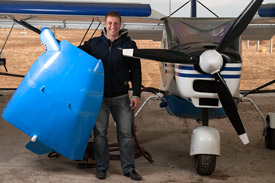
The pump assembly with fittings and couplings is attached to the shadow part of the back side of the chemical tank. The spraying fluid is continually mixed during a flight, which prevents sedimentation of heavy residues (e.g. humates) or crystallization of chemical agents, therefore increasing uniformity and quality of spraying.
As the pumps and fittings are located on the tank, it is very simple to convert the aircraft into the spraying version and back: just install or remove the tank and the booms.
Controls for the spraying equipment are placed inside the aircraft cockpit. When the switch “CHEM” on the aircraft instrument panel is activated, the pumps start continually agitating the spraying fluid inside the tank. The pilot can open and close RDA shutoff ball valves pushing a button located on the control stick without any interruption from piloting the aircraft. There is also a flowmeter display on the aircraft instrument panel, providing information on the discharge rate of the spraying fluid in liters per hectare and the amount of the fluid discharged in liters.
While flying, the pilot can adjust the flow rate using a handle located under the thrust lever that allows opening or closing the tank mixing valve; the flowmeter display will show the changing parameters.
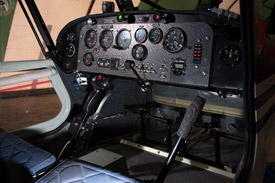
Preparation of spraying material involves a land-based filling system comprising a petrol engine driven pump with a filter and a plastic barrel with a chemically resistant hose. Hydraulic agitation and filtration provided by the system allow a technician to prepare spraying material while the aircraft is still in the air, and upon the aircraft’s landing it will take about one minute and a half to fill the aircraft chemical tank with filtrated spraying fluid.
This spraying system has been installed and has been efficiently working on aircrafts of the following companies: Agrolet (Volgograd, Russia), Aeron (Saratov, Russia), Yuzhny Aviatsionny Center (Volgograd, Russia), Klyuchnikov (Volgodonsk, Russia), Pasikov (Volgodonsk, Russia), Kuratov (Novosibirsk, Russia), V.S. Popov (Blagoveschensk, Russia), Sosnovka-Zernoprodukt (Tambov, Russia).
Should any questions concerning the spraying equipment and parts arise, please contact us by email director@novatoravia.ru, lygin@novatoravia.ru
or by phone +7-905-330-1119, +7-903-377-8222.
